8 Trucking KPIs to Track (+ How to Calculate)
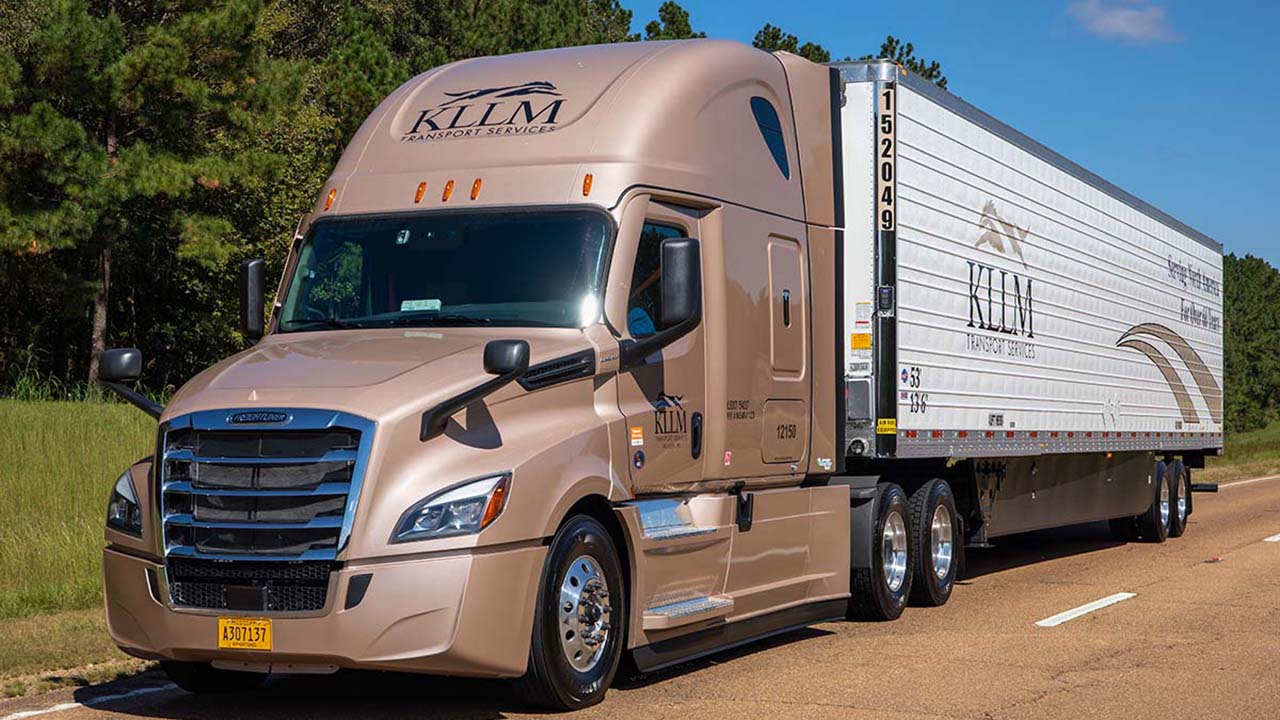
The trucking industry sector is very competitive, requiring any trucking business owner to track specific metrics (KPIs) to grow while maintaining profitability. With significant upfront capex and high operating costs, it’s even more relevant than ever for trucking companies to measure and track certain KPIs to maximise growth and profitability.
From cost per mile, OTD, deadhead rate, maintenance downtime, etc. this article discusses the 8 most important KPIs any trucking company must track. Let’s dive in!
1. On-Time Delivery (OTD)
This is one of the most important KPIs trucking companies should measure because it indicates whether you are delivering shipments to clients on time. Expressed as a percentage, the metric measures the speed with which the company operates to meet required targets.
Tracking OTD can help your business identify inefficiencies and retain customers. Therefore, always aim to have a high OTD percentage since it can enhance the business’s reliability and reflect positively on the team’s bandwidth.
To calculate OTD, you divide the number of deliveries made in time by the total deliveries.
OTD = shipments delivered on time / total deliveries
where
Shipments delivered on time = Delivered shipments – Late shipments
For instance, if you delivered 1,000 shipments and 17 of the shipments were late, then your OTD will be:
OTD = 983 / 1,000 = 98.3%
2. Cost per Mile (CPM)
This is another important KPI trucking businesses should track since it gives the cost of hauling a shipment per mile. It is advisable to track this KPI at least each month. If you know the cost per mile, it is easier to determine the breakeven cost by multiplying CPM by the distance of the haul and then multiplying the cost by the target profit percentage to get a bid.
To determine CPM, you add all operating and overhead costs and divide by the number of miles covered (both empty and loaded miles).
CPM = Total costs / Total miles covered
For instance, if your truck covers 8,542 miles in a month and total costs (variable, fixed, and driver’s wage costs) are $12,325, then:
CPM = $12,325 / 8,542 = $1.44 per mile
3. Average miles per gallon (MPG)
This is a crucial KPI trucking business should track to understand how much fuel your trucks are using per mile. Understanding how much you spend per mile on fuel is important in booking profitable shipments. In addition, you should determine your trucks’ fuel efficiency to calculate revenue, profit, and cost per mile.
If you know the miles per gallon, the trucks get, and the fuel cost, it is possible to predict the cost of shipping a load over a certain distance. As a result, this can help you set your bid for budgeting purposes.
MPG = Total miles driven / # of gallons used
For instance, if your truck drives 1,083 miles and uses 190 gallons of diesel, then MPG will be;
MPG = 1,083 / 190 = 5.7 miles per gallon
4. Utilization rate
Utilization rate is another of the important KPIs to measure for trucking businesses. It measures the percentage of a specific truck (or a fleet) efficiency in terms of the miles driven.
The utilization rate is the difference between the total truck mileage capacity relative to the actual mileage covered.
Fleet utilization rate = total fleet miles driven / total mileage capacity
where
Total mileage capacity = number of trucks x average miles per driver
For instance, if you have 10 trucks and, on average a driver drives 1,082 miles. If in a month a specific truck travel 8,560 miles, then this truck’s utilization rate will be:
Fleet utilization rate = 8,560 / (10 x 1,082) = 79%
5. Deadhead miles
Deadhead or empty miles are the miles the truck travels without a load. This is irrespective of whether the driver will pick up a load or has dropped off one and is returning empty. Tracking this KPI is vital since the truck will use resources like fuel and driver time without generating direct revenue.
Therefore, tracking this KPI can offer insight into the routes causing dead miles, allowing you to optimize route scheduling and resource allocation. The secret is planning carefully, so drivers travel short distances without load to minimize costs.
Deadhead miles = Total miles – Paid miles
and
Deadhead rate = Deadhead miles / Total miles
For instance, if your trucks cover 10,820 miles in a month and only 8,560 miles are paid, then deadhead miles will be:
Deadhead miles = 18,820 – 8,560 = 2,260
and
Deadhead rate = 2,260 / 18,820 = 12%
6. Route Adherence
You should be aware of whether drivers follow the planned routes. You may distinguish between drivers who legitimately get lost and those who purposefully veer off the road to perform errands by comparing their path with an optimum route.
You can easily track the drivers’ inefficiency using a GPS tracking system to address inefficiencies as soon as possible.
If drivers don’t follow their scheduled route, they can lead to delays in delivery or falling behind schedule. You can increase productivity throughout each stage of the transportation and last-mile cycle by utilizing the delivery cycle of planning, route optimization, hauling, and tracking systems.
Route adherence is often referred to as a percentage that tracks a vehicle’s GPS position and compares the miles it drove as per the route vs. the miles driven outside the original planned route.
7. Total Cost Ownership (TCO)
This is a total cost indicator for the business that accounts for the initial cost of the truck, its fuel usage, its repair, and other costs associated with owning and using the vehicle, such as licenses, taxes, storage fees, etc.
You may need to track TCO for specific fleet assets and compare it to its income to find areas where cost savings can be made.
Most importantly, TCO is used by all trucking and transport companies worldwide to assess which vehicle to purchase in light of all the expected costs it will incur over its lifespan (before it’s sold to another buyer).
TCO = Purchase Price + Total costs incurred during lifespan
For instance, if the cost of acquiring a truck is $150,000, yet total maintenance costs are $15,000 per year for a lifespan of 12 years, then TCO is:
TCO = $160,000 + $180,000 = $340,000
8. Maintenance downtime
Keep an eye out for trends in maintenance downtime, particularly if you use older vehicles. If there are extended downtimes, you might need to rent a different unit or not submit a bid for some assignments. You’ll be made aware of these choices by monitoring this measure, which may mean modifying your yearly income targets.
Whether it is an in-house maintenance crew or you outsource repairs, it is crucial to minimize downtime for repairs.
Maintenance downtime = Grounded time / Total operating time
For instance, if your truck is to operate from Monday to Friday and it stays grounded for 10 consecutive days (2 weekends) for maintenance in a month, then downtime will be:
Maintenance downtime = 10 / 20 = 30%